Table of contents
Whether a manufacturing company is using the MRP function in the ERP system or an advanced supply chain planning solution, reviewing the exceptions produced during the planning process is a tedious but critical task. Failure to address a single exception message can lead to a late customer order or a production line shutdown. With such dire consequences looming, planners dive into the exceptions list, prioritize near-term exceptions, and get to work following up with internal functions and suppliers. But, why are there always so many exception messages? Why do so many exceptions recur? And with so many exceptions, is it possible to understand supply accuracy?
There are many root causes for large numbers of exceptions that confront planners after each planning run:
- Supply chain volatility, including customer order changes, late purchase orders, out-of-stocks, order cancellations, unexpected demand, material shortages, supply disruptions, and transportation delays
- Manufacturing variability, including work center and equipment breakdowns, lack of capacity, labor shortages, plant efficiency and utilization, yield and quality problems, learning curve and operator proficiency allowances
- Inaccurate inventory and production status, including on-hand inventory, work-in-process, expiry, batch and lot control, receiving status, purchase order status, and quality holds
- Inaccurate planning parameters, including those related to lead times, minimum order quantities, safety stock, economic order quantities, supplier splits, forecasts, forecast consumption, resource capacities, runtimes, and shop routing sequences
- Inaccurate master data, including missing bills of materials (BOM), incorrect part numbers or quantities on BOMs, supplier and customer information errors, and part master data issues including units of measures and conversions
If armed with the right tools to respond to them, many of these exceptions are preventable and the remaining exceptions, largely a result of supply chain volatility, can be mitigated (see Table 1). For planners responsible for resolving exceptions as a daily routine, it may be hard to understand where the data will come from to prevent future exceptions. After all, it is usually not even possible to review all exceptions before the next planning run creates an entirely new list. There is never enough time to collect data on each exception or to research exceptions to identify why some—those attributed to a specific supplier or those stemming from a specific product or product line, for example—recur frequently.
Exception Category |
Resolution Approach |
Inaccurate master data |
Prevent |
Inaccurate planning parameters |
Prevent |
Inaccurate inventory and production status |
Prevent |
Manufacturing variability |
Mitigate |
Supply chain volatility |
Mitigate |
TraceLink Supply Chain Work Management can not only streamline the exception management process, it can also provide the data and visibility you need to identify recurring exceptions. As planners use Supply Chain Work Management to collaborate with internal teams and suppliers to resolve exceptions, it is also collecting data from the subject matter experts engaged in the resolution process. This data includes the exception message description, the supplier, the immediate resolution, and the root cause (if identified during the process) or potential root cause (if a subject matter expert is providing an educated guess). This data is retained after the exception is closed to support continuous improvement projects designed to address preventable exceptions.
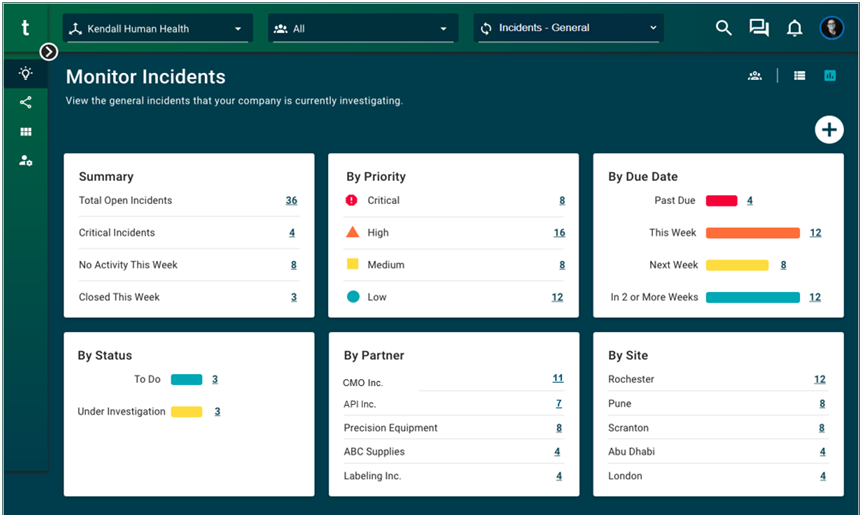
Real-time dashboards provide visibility to managers, planners, and suppliers, planners, and suppliers, enabling them to organize exceptions by priority and/or due date to keep everyone aligned on the most critical follow-up required. Dashboards also enable planners to easily view suppliers with the most open exceptions. A quick review of suppliers at the top of the By Partner panel may identify systemic issues such as wrong lead times or capacity problems.
Faster resolution means more time to prevent exceptions
Companies using Supply Chain Work Management have reduced exception resolution time by as much 65%. This improvement in resolution time is achieved almost immediately as suppliers are instantly notified and resolution due dates are set to ensure prompt attention. Lengthy email and phone-based exception resolution processes are replaced by a shared, collaborative work management process.
With collaborative work management, a cross-functional team is engaged in the resolution process and can help identify preventable exceptions. For example, a plant manager at the supplier that agrees to expedite a production order that is related to a late purchase order may not be aware that the order was received without the required lead time. Engaging the supplier’s planner or customer service rep would more likely uncover this detail. With a better understanding of the supplier’s required lead time, the planner can prevent future exceptions with a simple ERP system update.
This is an example of an inaccurate planning parameter. Supply Chain Work Management resolution history data provides a rich source of information to identify the causes behind many of the preventable exceptions. While some of the causes will be identified and addressed during the resolution process, other causes may require further investigation. Identifying recurring exceptions that result from inaccurate master data, and planning parameters can lead to a large reduction in exceptions. Considering the thousands of data elements used by the planning process and the subsequent generation of purchase and work orders, inaccurate data is inevitable. Finding it and permanently fixing it is best done through a continuous improvement methodology such as Six Sigma DMAIC supported by resolution history. Companies using Supply Chain Work Management resolution history data to support the define, measure, and analyze steps of Six Sigma DMAIC have reduced defects per million by as much as 96%.
More time to focus on supply accuracy
Systematically reducing preventable exceptions gives planners more time to focus on supply accuracy by mitigating the impact of supply chain volatility and manufacturing variability exceptions. In the demand planning process, the accuracy of the demand plan is measured by forecast error. While the supply plan has no formal accuracy measurement, the number of exceptions can be used as a measurement of supply accuracy. While general market volatility will always create exceptions, too many exceptions indicate that the supply plan and the supply chain are not aligned—supply accuracy is inversely related to the number of exceptions. With preventable exceptions out of the way, planners can begin to focus on the more complex issues that lead to supply problems. The exception management capabilities of most planning systems treat each exception as a discrete event and do not make it easy to determine aggregate supply accuracy. For this reason, many planners will download exceptions into Excel for further analysis. Excel, however, does not help with supply planning’s biggest blind spot: exception follow-up and confirmation with suppliers.
With exceptions managed in Supply Chain Work Management, suppliers are immediately aware of changes to open purchase orders and become an active part of the exception management process. From the dashboards in Supply Chain Work Management, planners can identify suppliers with the most open exceptions, which is an early indicator of potential supply disruptions. Similarly, the By Due Date panel on the dashboard enables planners and suppliers to identify exceptions that are overdue and may also lead to supply disruptions. While suppliers may not always be able to comply with requested purchase order changes, supply accuracy will improve as planners get much better visibility to what the supply will be and can adjust the plan accordingly.
As with the preventable exceptions, the collaborative resolution process and the retained history will provide valuable data to identify weak supply chain processes that result in too many exceptions and contribute to poor supply accuracy. With a collaborative resolution process driven by subject matter experts, Supply Chain Work Management makes it more likely that the root causes of supply accuracy problems are identified. For example, a supplier’s inability to accommodate a purchase order change may be related to understated forecasts shared with the supplier that make it impossible to accommodate unexpected order quantity increases. Once identified, this is a problem that the planning team can address. On the other hand, the root cause may be that the supplier lacks the agility to keep up with regular market dynamics. This becomes a problem for the supplier management team to address.
Irrespective of whether the root cause of the exception is internal or external, it is important that the process be improved to prevent exceptions from recurring. Fewer exceptions mean better production and supply plans which leads to more efficient manufacturing operations and improved on-time, in-full supplier performance. Supply chain teams using Supply Chain Work Management to address recurring exceptions have seen as much as an 82% improvement in customer delivery performance.
TraceLink Supply Chain Work Management is a quick and easy way to harness the power of the planning team’s and the suppliers’ expertise so you can successfully navigate supply chain disruptions and improve supply accuracy. More predictable supply makes it easier for the commercial team to acquire new customers and grow revenue.
Learn more in our Supply Chain Work Management Resource Center.