Table of contents
Key Takeaways
- Material shortages and late shipments are seen as the most significant sources of supply chain cost and risk.
- Collaborative multienterprise work management software can help manufacturing organizations overcome all types of supply chain risks.
Late shipments and material shortages are the biggest sources of supply chain risk and cost for manufacturing organizations, according to a recent executive survey conducted by Gatepoint Research on behalf of TraceLink.
The survey of 105 company leaders—including managers, directors, vice presidents, and C-level executives—found that quality defects, contract manufacturer production delays, and out-of-specification process controls round out the top five threats to on-time, in-full delivery performance.
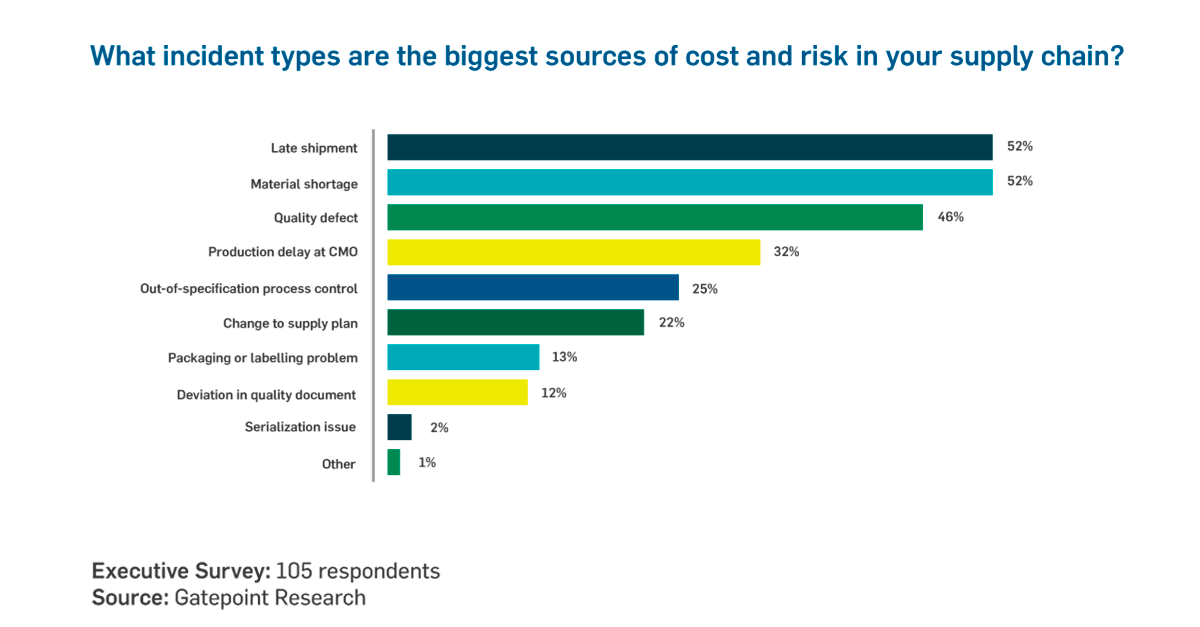
Additional sources of supply chain risk and cost include changes to supply plans, labelling and packaging problems, quality document issues, and to a lesser extent, serialization and compliance issues.
Why does it take so long to resolve supply chain issues?
The survey also revealed that the top challenges to effective supply chain issue management include lengthy incident response and resolution processes; managing recurring issues with the same suppliers; and a lack of real-time visibility into issues resolution processes.
Collaborative multienterprise work management software brings speed, accountability, structure, and to supply chain issue management processes—and it’s been proven to help manufacturers reduce supply chain risk and resolve issues up to 65% faster.
Resolving supply chain issues like late shipments and material shortages can take an average of five to six weeks or longer. This is largely due to a lack of structured, digitized processes for collaborating on and executing shared work with supply chain partners. Additional reasons resolving supply chain issues tends to be a lengthy and cumbersome process include:
- Unclear incident resolution process
- Dependence on unstructured collaboration tools like phone calls, emails, and video meetings
- No institutional memory to support continuous improvement
- Failure to identify issues early
- Failure to rapidly get the right people involved in issue resolution processes
The good news is that digital supply networks and collaborative, multienterprise work management solutions are speeding up and increasing the efficiency of supply chain issue management processes.
Resolve issues 65% faster with multienterprise work management
Collaborative multienterprise work management software brings speed, accountability, structure, and to supply chain issue management processes—and it’s been proven to help manufacturers reduce supply chain risk and resolve issues up to 65% faster. With multienterprise work management software, supply chain and procurement teams can:
- Gain centralized visibility
- Perform root cause analysis
- Apply an efficient, workflow-driven process with clear roles and accountabilities
- Ensure the right people are quickly notified when issues arise
- Add structured to traditionally unstructured collaboration processes
Supply chain issue management is a multienterprise process that has not been digitalized in most organizations. Companies that digitalize and streamline their supply chains with collaborative multienterprise work management software can resolve issues faster, support continuous business process improvement efforts, reduce recurring issues, and dramatically improve supply chain performance.
Download our new handbook for more information on supply chain issue management.
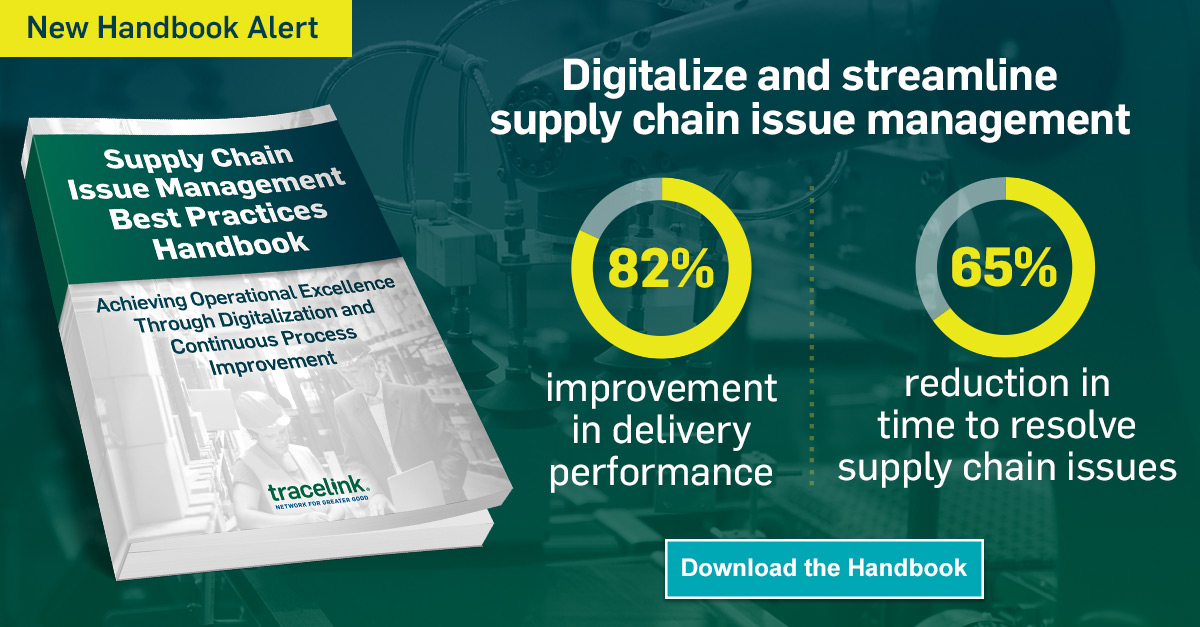