Table of contents
Key Takeaways
- This pandemic continues to test the pharmaceutical supply chain at every point.
- Companies are re-assessing supply chain models and accelerating digital supply chain initiatives.
- Visibility, transparency, and real-time data will be required to face new challenges more effectively.
By Shabbir Dahod | April 3, 2020
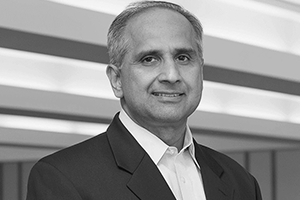
Over the past week, I’ve spoken with TraceLink customers from around the world, and I can safely say that not one of them has been untouched by—or is unconcerned with—the effect that the COVID-19 pandemic is having on their patients, partners, employees, and businesses.
It may also be safe to say that we will look back on these weeks and months and divide the history of our industry into “before” and “after” COVID-19. This pandemic continues to test the pharmaceutical supply chain at every point in the process, from supplier to dispenser. It has challenged the models, outpaced forecasts, and elicited new and unexpected behaviors in the market as companies and consumers try to make sense of a fast-changing and uncertain situation.
Meeting a “force majeure” head-on requires an agile supply chain
From their forward positions on the front lines, the companies I’ve spoken with have impressed me with their grasp of the situation as they implement a rapid, real-time re-prioritization and mobilization of resources. The challenges they are facing are significant: A suddenly remote workforce. IT and communications systems pushed to their limits. Normally reliable sources going offline. Critical ingredients in short supply. Three-month inventories turning into shortages. And air and ground transportation being diverted or grounded.
Every customer had a story to tell, but they all followed a common theme: These are not normal times, but what will the “next normal” look like after we have met this challenge? The supply chain executives I spoke with pointed to the need for greater visibility and transparency—especially at the supplier and manufacturer level—and for real-time data to make fast decisions and pivot quickly to face the unknown and unexpected.
The idea of digital transformation and its potential to create a more agile supply chain is no longer a question of “tell me why” but rather “tell me how.” The events of the past weeks and months are bringing several important issues to the forefront of customer concerns:
“Reliability and quality of information—and of planning—is key.”
As the early indicators pointed to a fast-developing pandemic, companies had to quickly assess how their ERP and business systems could respond to this potentially massive supply chain disruption. The COVID-19 pandemic has revealed critical gaps in how vital information about supplies, medicines, and equipment is captured and communicated. Until we have created a true “digital twin” of the physical supply chain, companies, agencies, and governments will continue to make life-or-death decisions based on non-real-time data, conflicting information, and “best guess” scenarios.
“We’re turning off the normal processes and re-evaluating how the supply chain is working.”
With the worldwide scramble for ingredients and products, companies needed the ability to find alternative sources, transportation routes, and distribution solutions. Several customers told us: the models aren’t holding up. I think this is, in fact, what the “next normal” will look like: A time of testing new scenarios and hypotheses that balance business sustainability and growth with crisis management and sudden shocks to the system. Companies will need to add additional sources and partners as quickly as possible to mitigate unexpected—and massive--supply disruptions.
“Coordination and communication between internal teams and external companies is harder given everyone is working remotely.”
Companies that are not moving their supply chain operations to the cloud may find themselves among the casualties of this pandemic. In little more than a week, a vast portion of the world’s population began to use online tools and platforms to work and communicate. All things considered, service levels have remained high, demonstrating the power of cloud-based solutions to scale rapidly and practically infinitely. Yet, for many companies, point-to-point connectivity issues and manual processes have hampered their efforts to authenticate, onboard, and ramp up new suppliers.
How can we continue to shape the future?
With this pandemic, we’re seeing the first major test of a supply chain in transition as many—but not all—companies are in the middle of digitalizing their supply chain operations. Supply chain agility, visibility, and transparency are now priorities both for pharmaceutical companies and their healthcare customers, who are extremely concerned about disruptions to the upstream supply chain and any eventual impact on critical supplies, equipment, and most of all, patients.
At the same time, we can’t lose sight of our shared responsibility for securing the supply chain in Russia, Brazil, Saudi Arabia, and the next wave of emerging markets around the world. Several customers pointed to the difficulty of maintaining their regulatory processes under extreme duress and demand. I see this as a false choice: no company should have to sacrifice patient safety in order to deliver critical medicines when and where they are most needed. TraceLink is committed to developing solutions that allow companies to do both, in parallel, as part of a holistic approach that delivers predictable results in unpredictable times.
With our network approaching 300,000 members, TraceLink enjoys a unique responsibility in advancing the digital supply chain. I look forward to speaking with more customers soon and will continue to share our collective insights. Meanwhile, let’s stay focused on the challenge and continue to work together, for greater good.
Shabbir Dahod is the President and Chief Executive Officer of TraceLink, Inc.
Return to: The Patient-Driven Supply Network