Table of contents
This pyramid visualizes the three essential capabilities required to prevent supply chain issues from escalating into supply chain disruptions:Companies that have digitalized supply chain issue management have seen significant supply chain performance improvements.
Working with internal teams and supply chain partners to resolve an issue can take five to six weeks or longer. Late shipments, material shortages, out-of-spec products, changes in production quantities, and other business processes and product quality defects often escalate into supply chain disruptions that result in late deliveries to customers.
Supply chain issue management is a business process that is best executed as a cross-company process. However, it has not been digitalized in most organizations, which hinders smooth issue management.
As a result, dealing with issues is often a firefighting exercise managed and resolved with unstructured and decentralized tools and processes like phone calls, emails, video conferencing, and spreadsheets. This means senior leaders often lack the visibility to respond to threats in the supply chain and much of the information needed to drive supply chain performance improvements is lost or never collected.
Have you ever dealt with a supply chain issue and said, “If I had only known sooner we could have done something about it?” TraceLink Supply Chain Work Management is a workflow-driven, multienterprise collaboration solution for capturing, analyzing, resolving, correcting, and preventing supply chain issues. Digitalizing the supply chain issue management process provides actionable visibility at all levels of the organization and across the end-to-end supply chain. With the TraceLink Supply Chain Work Management solution, you will never be caught by surprise when a supply chain issue strikes.
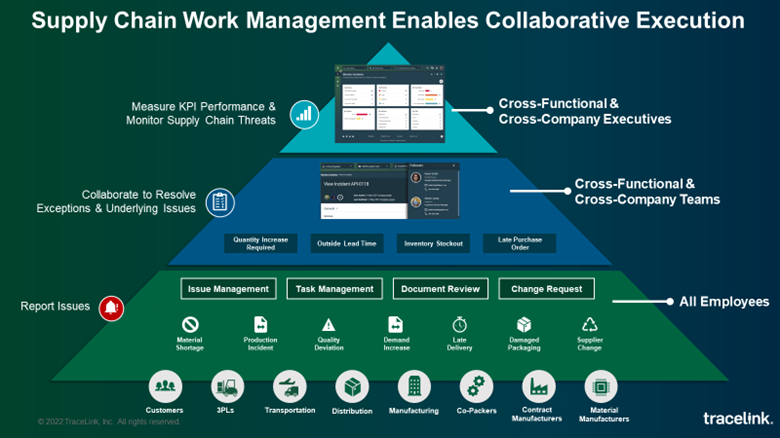
This pyramid visualizes the three essential capabilities required to prevent supply chain issues from escalating into supply chain disruptions:
Capability One: Actionable Issue Visibility for Managers and Executives Across the Extended Enterprise
Dashboards provide real-time visibility into all supply chain issues across the extended enterprise. Managers and executives at both your company and across your supply chain partners get full visibility into incidents, trends, and the resolution status. Unlike most scorecards that report on what happened in the past, dashboards provide status of active resolution processes. You and your supply chain partners work from a single source of shared truth as you collaborate to resolve issues. And leadership teams have the visibility they need to apply additional resources when the situation demands it.
Capability Two: Assign the Right Team of Subject Matter Experts
With Supply Chain Work Management, you can quickly drill into the incident and assign a member of the “process team” to ensure issues are routed to the right subject matter experts from inside and outside of your organization. Rapidly engaging with the right subject matter experts leads to faster issue resolution times. The increased clarity on user roles also helps organizations avoid reporting delays and ensures that issues are reported right away.
Capability Three: Enable Reporting of Issues Immediately Along With the Data Needed to Prioritize Resolution
All employees and supply chain partners can report issues as soon as they are identified and categorized, prioritize issues, and assign tasks and due dates. Purpose-built incident management processes bring structure to issue management to ensure that more complete definitions of issues are captured, including data related to quantitative and qualitative impact, analysis of the issue, and root cause identification. TraceLink Supply Chain Work Management supports five unique incident management processes as well as a process for managing change requests:
- Direct Material Supplier Incidents
- Indirect Materials Supplier Incidents
- External Manufacturing Incidents
- Internal Manufacturing Incidents
- General Incident
- Change Requests
The Benefits of Digitalizing Supply Chain Issue Management
One company that digitalized supply chain issue management saw significant supply chain performance improvements, including:
- 65% reduction in days to close an incident
- 35% reduction in incidents
- 50% reduction in repeat deviations
- 96% reduction in defects per million
- 97% reduction in manufacturing disruptions
- 82% improvement in delivery performance
These improvements in supply chain execution performance ultimately reduce costs and improve cash flows while reducing supply chain risk.
Learn more in our Supply Chain Work Management Resource Center.