Table of contents
APT-SCIM creates comprehensive incident definitions, provides complete visibility into resolution processes, and its collaborative root cause determination capability supports all types of process improvement projects.
Manufacturing organizations that digitalize supply chain issue management and resolution processes with a multienterprise collaboration solution—and use the data collected in that system to support continuous improvement methodologies such as Six Sigma—have reduced defects per million by as much as 96%.
This article provides a step-by-step guide to using TraceLink’s collaborative, multienterprise solution, Agile Process Teams for Supply Chain Issue Management (APT-SCIM), to support continuous business process improvement, dramatically reduce defects per million opportunities (DPMO), and reduce repeat deviations by as much as 50%. With APT-SCIM, organizations can:
● Rapidly identify recurring issues that should be targeted for improvement projects.
● Compare recurring issue project candidates by frequency and potential financial impact
● Analyze historical data to determine root causes
● Use change request capabilities to implement permanent improvements
● Monitor the outcome of projects with real-time dashboards.
5 steps to business process improvement success with APT-SCIM
APT-SCIM creates comprehensive incident definitions, provides complete visibility into resolution processes, and its collaborative root cause determination capability supports all types of process improvement projects. For example, here is a look at how organizations use APT-SCIM to support Six Sigma DMAIC continuous improvement projects:
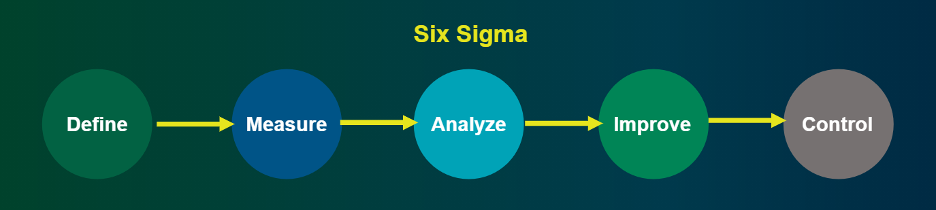
Step 1: Define
APT-SCIM empowers all internal team members and external supply chain partners to report incidents as soon as they occur. The solution guides users through a progression of easy-to-use dropdown lists to capture a complete definition of the issue. Teams can easily add new data collection fields to support the unique requirements of their organization and supply chain
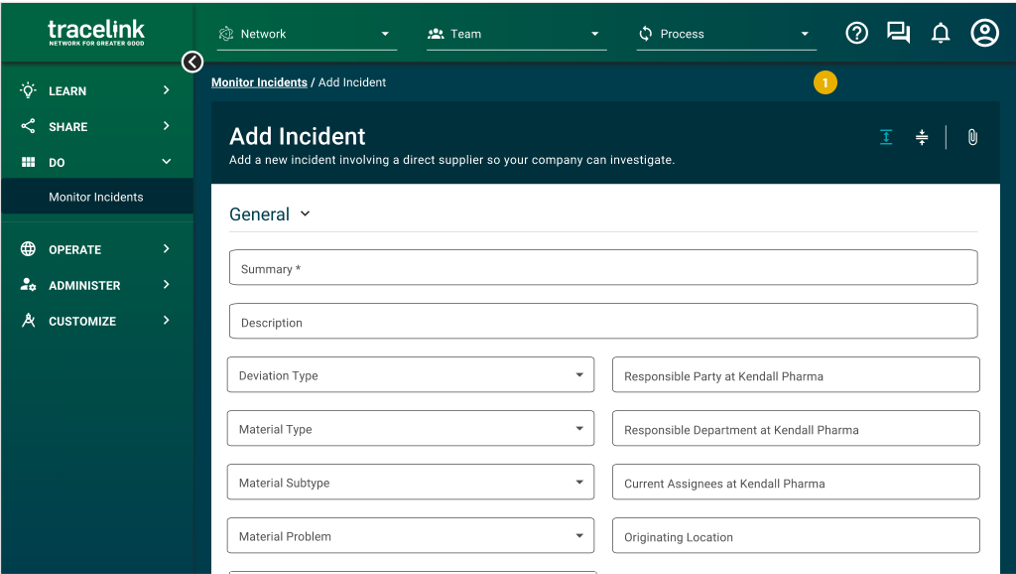
Step 2: Measure
APT-SCIM collects quantitative and qualitative values and leverages dashboards to help supply chain managers better understand troublesome internal processes, recurring issues, problematic partners that require help, and the severity of individual issues. With APT-SCIM, teams can collect and measure data related to things like number of issues, issue resolution times, financial impact, root causes, and the priority and severity of recurring issues.
Step 3: Analyze
Use issue resolution history and root cause assessments collected during the APT-SCIM incident management process to identify recurring and high-impact problems. APT-SCIM documents root causes during the incident resolution process for further analysis to identify repeat deviations
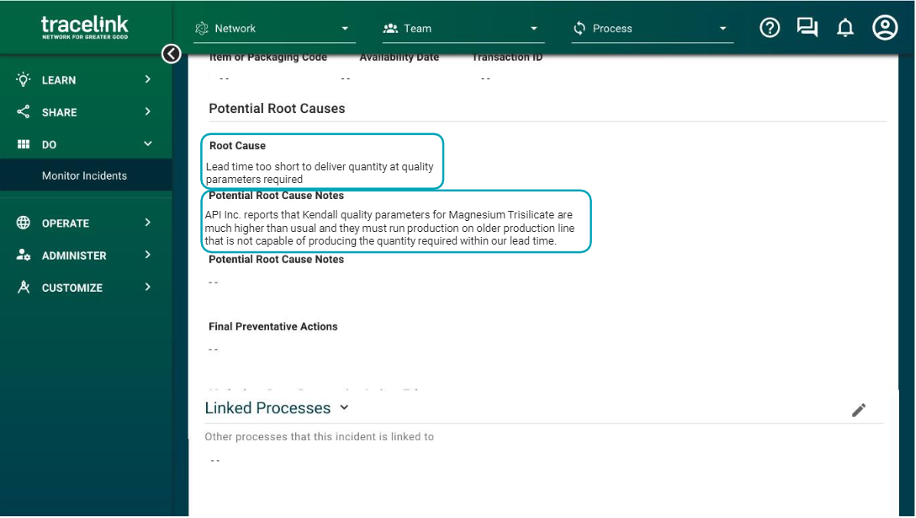
Step 4: Improve
Leverage the collaborative, virtual environment APT-SCIM provides to work closely with internal and external subject matter experts, develop corrective and preventative actions (CAPA), and implement permanent improvements.

Step 5: Control
Use configurable real-time dashboards to track partner performance and the effectiveness of business processes that have been modified. APT-SCIM gives supply chain teams the tools and data needed to determine defects per opportunities; identify the current number of defects; and set goals for reducing defects per million.
Eliminate recurring issues and reduce repeat deviations with APT-SCIM
Organizations get the most powerful results in terms of reducing repeat deviations when they target internal operations and supply chain partners with high incident counts. This leads to improved on-time, in-full delivery performance, a reduction in the cost of goods, increased revenue, and fewer supply chain disruptions.
Learn more in our Supply Chain Issue Management Resource Center.