Table of contents
Key Takeaways
-
The COVID-19 crisis will impact your supply chain and therefore your business.
- Supply chain leaders must lead the redefinition of supply chain business value.
- Business and supply chain leadership must lead the effort to change the mental model of "supply chain” to “patient-driven.”
By Roddy Martin | March 24, 2020
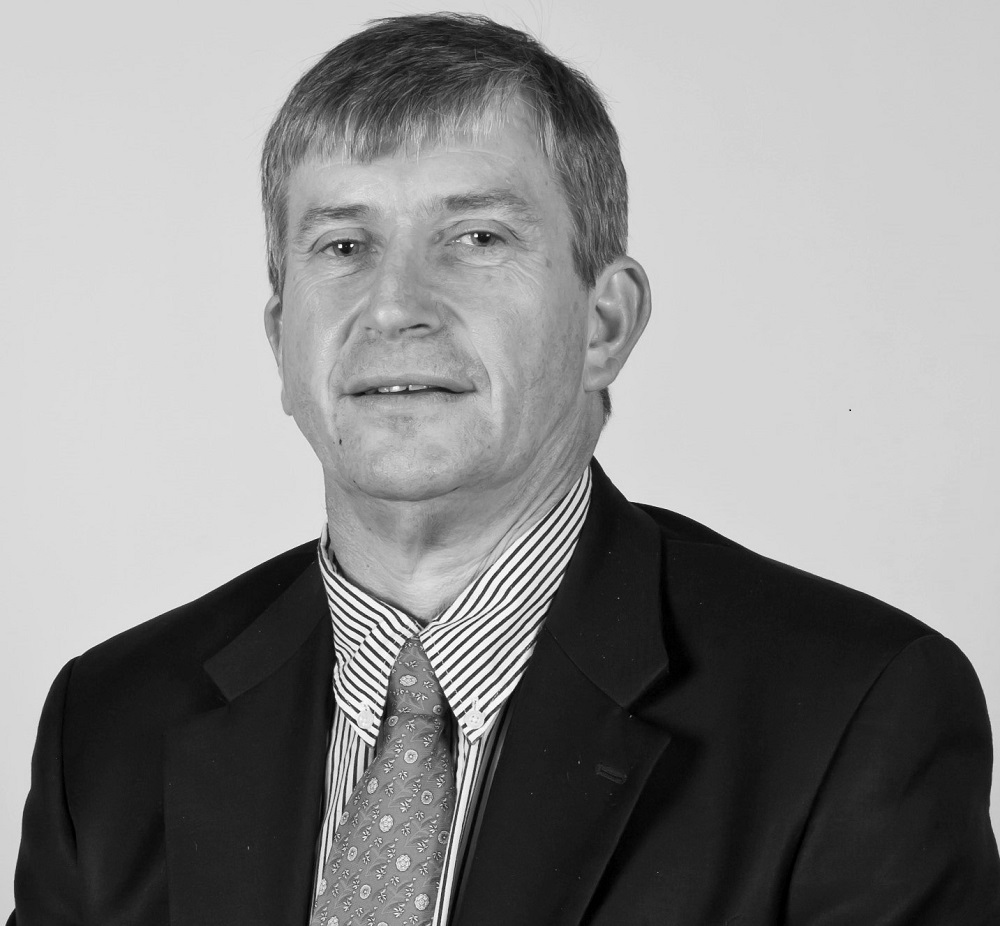
The urgency of the global COVID-19 crisis will impact every aspect of your supply chain and therefore your business. The time to reenergize and rebuild new end-to-end supply chain capabilities is now!
In part one of this article, I discussed major challenges facing supply chain leaders today, and the major steps needed to overcome them. Now let’s talk about how to get started on the transformation.
The key foundation is to redefine the business importance of your company’s supply chain in specific, patient-driven terms. For example, “always on time, in full (OTIF), right first time (RFT), safely to every patient.”
To mobilize action, start by changing the business’s mental model of “supply chain,” particularly among your business leadership peers who are not necessarily supply chain “savvy” but are all somehow implicated by this change.
The supply chain leader must step up as the catalyst and change agent for transformation. To get attention, emphasize that the supply chain is no longer simply about packing, shipping, and delivering activities that get products from the supply network to patients, the supply chain is now a business competitive weapon. This is not unique, and we have already seen companies like Apple make this transformation.
Today’s reality is that with COVID-19 your business is now probably operating with unique capacity and supply constraints in every sense. As a supply chain leader, the business will look to you to lead a working, compliant, reliable patient-focused supply chain across the business. Realize that in today’s situation this may mean the survival of your company.
Here is a three-step guide to getting started:
First: Change the supply chain mental model
Today’s business and supply chain design starts with the patient. This is not as it always has been. Historically, pharma companies made hundreds of days of inventory and buffered it across the supply chain to guarantee broad supply to downstream partners. Switching to an end-to-end, patient-driven approach is complex because it involves changing old cultures, behaviors, systems, and metrics, and may even mean changing leadership. Look forward and start the change now because it will become increasingly difficult as personalized medicine business models such as cell and gene therapy processes that are focused on designing products and services for individual patients become increasingly common.
Action item: Get your business, especially the leadership team, to rally around redefined critical supply chain capabilities. Get them to understand that the supply chain is the end-to-end business operating model starting at the patient and must be continuously transparent with actionable visibility of any disruptions. All resource and planning tradeoffs made between supply and demand balancing must be made with orchestrated patient-outcomes in mind, not just on driving business revenues and profits.
This probably means reorganizing supply chain teams and combining them with business, sales, and IT specialists focused on orchestrating patient outcomes and patient supply performance analyses. It’s time to re-energize the business around the new supply chain, starting today and with everyone on the same page and agenda!
Second: Drive for patient OTIF
Do a thorough analysis of all disruptive events and issues occurring in the end-to-end healthcare supply chain from the patient to the manufacturing and supply of compliant product. Surface, capture, and analyze (with data and context) all those issues and events that impact delivery and availability to downstream partners and ultimately to patients. This means systematically analyzing all the reasons why delivery to the patient did not meet OTIF and RFT patient safety goals.
Remember: As a supply chain leader doing this analysis with your business team, you will need to cross many different downstream boundaries—organizational units, partners, systems, and processes, inside and outside the business—from supply all the way to the patient. This may be a challenge in itself, because outside of planning and logistics, the supply chain has not always had credibility in downstream customer and patient-facing supply chain processes.
Action item: Perform integrative, value-based root cause analyses and group the list of these disruptive supply chain issues and events traced in the end-to-end supply chain. Build a prioritized portfolio list of these issues so that they can be continuously tracked, analyzed, and eliminated in a top down, cross-functional governance leadership structure. Aggressively focus on this prioritized list and report status on an ongoing basis so that the business sees the value and progress of the effort and can participate in the momentum of transforming the supply chain.
In this process, ensure that you keep the value stream analyses process and improvement integrative so that finding and fixing problems in one area doesn’t just move the problem around the supply chain to another area. This happens when the processes and solutions are individualistic, disconnected, siloed, and fragmented. Make sure that solutions holistically consider all the key people, process, and technology elements to be sustainable.
Third: Start and lead the deployment of your digital operating model capabilities
There has never been a better time to urgently digitalize and interconnect your business internally and externally to partners on the network. We have long spoken about creating a digital twin of the end-to-end business and supply chain, a digital view of the operating business that is real time, accurate, and data based. The same sense of urgency exists now to start your digital transformation.
Action item: After digitally connecting to partners on the network, use aggregated data and digital augmented analytics capabilities to find and analyze the problems, issues, and disconnects in the end-to-end, patient-facing supply chain. In the value stream analyses, you are likely to find issues that you didn’t even know existed.
Take a stand with technology leadership to lead the discovery and choice of a new digital network platform for the business. The reality is that the traditional integrated, end-to-end linear-connected IT model, and the complex architecture of traditional IT applications like ERP and planning systems, no longer meet the agility needed to be continuously responsive to patients.
Now is the time to drive improvement
Although no one wants to see a crisis like the COVID-19 pandemic unfold any further, dramatic events like this that pose high risks to patients, governments, and industries are an urgent catalyst for transformation. They are very visible to executive leadership in the business and command survival attention.
Now is the time for supply chain leaders and teams to step up and take a stake in more business leadership change management roles.
One last piece of advice: Analyze your business model and value streams from the “patient back to supply,” not just “product supply to the patient.” This forces the business to focus on what’s critical to patients and not just what’s possible to achieve with excess inventory safety buffers.
Strive for the type of “patient-driven supply network” capabilities touted by thought leader Alessandro De Luca, CIO of Merck Healthcare at Merck Group and former member of P&G’s supply chain transformation.
Roddy Martin is Chief Digital Transformation Officer at TraceLink.
Return to: The Patient-Driven Supply Network