Table of contents
Key Takeaways
- When disruption strikes, you need visibility into the HERE and NOW—not the past.
- Effective re-planning requires end-to-end supply chain engagement and communication.
- Regulations, precision materials, and controlled conditions make the pharma supply chain especially prone to delays and disruptions.
By John Bermudez | August 7, 2020
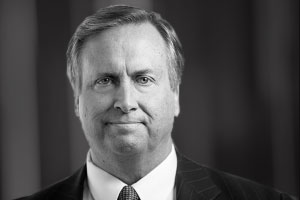
When families plan a beach vacation, they count on optimal conditions: sunny days, plenty of parking, and shark-free waters. But a stretch of bad weather or a shark-related beach closure requires on-the-spot thinking and a new plan. For supply chain managers, the global pandemic has become their “shark attack” with unanticipated disruptions as hard to predict as beach closures. A huge spike in demand for one product, a plunge in demand for another product, a local lock down, and constantly changing government regulations are just a few of the new disruptions impacting pharmaceutical manufacturers’ global supply chain, their plans—and often their contingency plans as well—can suddenly give way to an all-hands re-planning effort.
When that happens, the question is: What do supply chain managers need visibility into when things don’t go as planned?
The parameters that drive the supply chain haven’t changed all that much in the last 20 years. Demand forecasts, customer orders, and available inventory are still the primary inputs used by ERPs or supply chain planning systems to generate purchase orders, production orders, and ASNs.
But when plans are disrupted and orders need to be updated, supply chain managers don’t need more visibility into data that they've already sent to their suppliers. They need up-to-the-moment visibility into the issues and events—outside of their four walls—that threaten on-time, in-full delivery, such as:
- A key supplier forced offline by an approaching monsoon.
- A local government-mandated lock down for non-essential businesses—and your packaging material plant was considered non-essential.
- A critical raw material that won’t be received in time.
- A production line shut down due to a worker being infected with COVID-19.
- A sudden and significant increase in customer demand.
- An unforseen drop in production yields and lower quantities of ready-to-ship product.
- Approvals and change orders needed to get API from new secondary sources.
- A batch sent for batch record review without a proper Certificate of Analysis (CoA).
- A batch record review delayed because the approver is on vacation.
- A production line shutdown pending an order to change a feeding tube on a tablet press from 316 SS to plastic.
Any one of these issues can cause lengthy delays, late shipments, and unhappy customers, and some may trigger other issues that ripple across the entire network of suppliers. Whether a supply chain manager is calculating the impact of a disruption on a whiteboard or using an algorithm-based replanning tool, they need a complete picture—which requires input from internal and external teams of domain experts—to get answers to pressing questions, such as:
- How real is that monsoon threat? Does the supplier have a contingency plan?
- How long is the mandated local lock down that has forced a plant closure expected to be? Will the plant be allowed to reopen with a reduced staff?
- Customer demand is suddenly way up. Is this a temporary blip or a permanent trend? The planning system can increase quantities, but can suppliers deliver?
- Are there trade-offs with shared API or production capacity? What orders or products don’t get produced? Can we maintain production if we agree to overtime?
This is when the four walls suddenly begin to close in. Even if internal teams have been mobilized to respond to a disruption, information gaps and unstructured, ad hoc processes using emails and phone calls prevent you from getting timely input from suppliers on various alternatives to resolve the incident. For effective re-planning, it’s critical to
- identify the immediate problem;
- understand the alternative resolutions;
- adjust and communicate plans; and
- coordinate a multi-enterprise response that aligns internal teams and external partners.
Before you plug in a new set of numbers, plug into your supply network
Effective re-planning involves more than simply inputting a new set of updated order quantities, due dates, and other “numbers” into a planning system—especially for the pharma supply chain, where stringent quality and safety measures, complex choreography between direct and indirect materials, controlled storage conditions, and regulatory oversight introduce a much wider set of parameters and variables into the manufacturing process.
Purpose-built to identify, categorize, track, and manage life sciences supply chain incidents, TraceLink’s Agile Process Teams enables multi-enterprise collaboration and gives supply chain managers the end-to-end visibility they need to assess the severity of an incident and develop a solution. When used in concert with your ERP system or concurrent planning solution to respond to a disruption, Agile Process Teams gives you the complete picture needed to ensure a more effective re-planning effort.
Beyond helping you respond to disruptive incidents such as material shortages and quality deviations, Agile Process Teams also provides a comprehensive history of incidents that can be used to evaluate supplier performance, improve right-first-time quality levels, drive continuous improvement efforts, and support more agile scenario development and planning. Agile Process Teams needs to be an essential component of your crisis response toolkit.
Digital pioneers wanted: Join the Agile Process Teams Innovation Forum
I invite you to join TraceLink’s newest Cloud Community Forum and help us define the future capabilities of Agile Process Teams. Our goal is to identify multi-company use cases where better intercompany collaborative processes can help companies respond more effectively to supply chain disruptions.
Email me at jbermudez [at] tracelink.com (jbermudez[at]tracelink[dot]com) and I will send you an invitation to the next meeting of the Agile Process Teams Innovation Forum.