Table of contents
Key Takeaways
- COVID-19 has sparked a renewed conversation about supply chain agility and resilience.
- Reliability and predictiability are key components of supply chain agility.
- It's important to view supply chain disruptions through the eyes of the patient.
By Roddy Martin | July 6, 2020
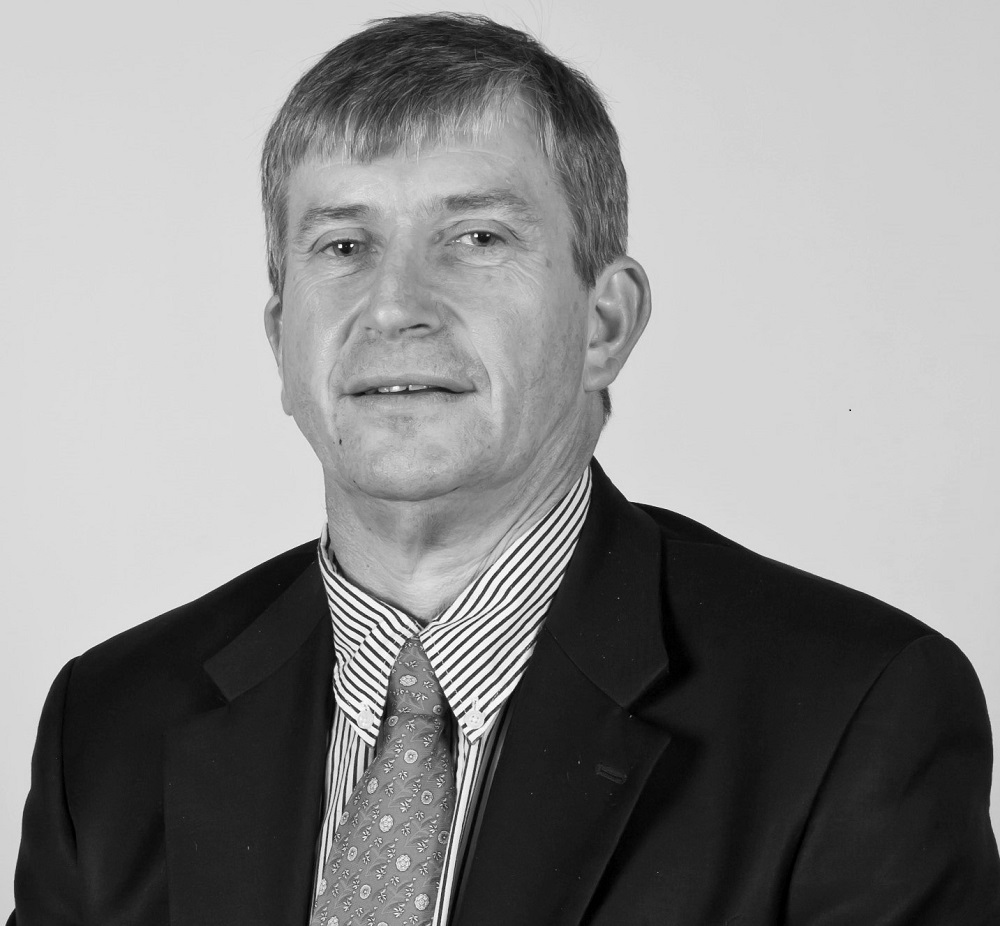
The word “agile” was commonly heard in supply chain and manufacturing circles 20 years ago. Back then it was about building the agility to manufacture with varying lead times and volumes to deliver a broad range of products and services that met customer demand. Flexibility and lean were often used in the same sentence and the model was largely “inside-out, supply-driven.”
Today, we are seeing a resurgence in the supply chain use of “agility,” but this time in conjunction with "resilience." This is because agility and resilience are the capabilities that were largely missing in the global responsiveness to disruptions that characterized the COVID-19 pandemic.
This time the use of agile and resilience is more “outside-in, demand-driven,” and it’s about smart responsiveness that can rapidly adapt to varying demand needs in a constrained supply system despite supply chain disruptions. This is what an agile and resilient response to COVID-19 is all about!
The virtual supply chain thought leader panel
A virtual LogiPharma panel of supply chain thought leaders took place recently instead of a planned live event in Nice, France. The panel brought together more than 100 years of global thought leadership and executive level supply chain experience. I served as the moderator and additional guests on the auspicious panel included:
- Professor Hau Lee of Stanford University Business School
- Mike Wittman, executive supply chain consultant and former supply chain leader at Mars, Johnson & Johnson, and Pinnacle Foods.
- Paul McKenzie, Chief Operating Officer of CSL Behring and a former supply chain leader at Johnson & Johnson, Merck, and Biogen.
- Paul Bittinger, formerly of Procter & Gamble and Nature’s Bounty Operations Excellence and Operations Leadership.
The panel was truly a deep “wow” of supply chain experience!
We started with Paul McKenzie calling out a special thank you for global essential services given to support the COVID-19 pandemic.
The supply chain scene was set by Prof Hau Lee; the infamous “father” of the “bullwhip effect” that characterizes distorted supply chain data and response in disruptive supply chain scenarios. Hau Lee put forward that this pandemic highlighted the need for supply chain “hyper-agility,” orders of magnitude more than just the agility needed to deal with past natural disruptions such as the 2011 earthquake that hit Japan.
Professor Hau Lee’s hyper-agility need significantly ratcheted up the need for a visibility network that elevated end-to-end speed, flexibility, contextual information, analyses, and responsiveness capabilities like never before. He made the important point that without smart, intelligent, and actionable sensing and visibility, the agility needed to intelligently sense and respond to disruptions and minimize their impact on the business and downstream demand points, where customers and patients have real needs, was not achievable without chaos.
Paul McKenzie said that the pandemic had tested all facets of his business’s global “continuity planning” and “what if” scenario planning capabilities at all levels. Previous supply chain disruptions required flexing of one or more of the business’s muscles, but this pandemic required the orchestrated global and simultaneous flexing of all business muscles to ensure responsiveness. This called for continuous learning and adapting of the plans as the pandemic dynamically evolved over the global business stage at a pace never seen before. To survive, businesses had to learn on the fly to act locally and think globally with critically strong top-down leadership across the business.
Mike Wittman emphasized that the complexity and traditional complacency in pharma shouldn’t be underestimated when building agility because they are traditionally slow to react given the nature of their business. He said an intentional and specific focus had to be placed on supply chain reliability because it isn’t possible to build sustainable agility and resilience to disruption with intelligent visibility without a solid basis of supply chain reliability on both the demand and execution side of the supply chain. He cited his experience in a medium-size manufacturing site with thousands of potential failure points where it is important to conduct an end-to-end process and risk analyses to surface a business continuity and risk management plan in case of disruptions. It is important to realize that not every possible failure scenario can be addressed, and a critical patient-back analyses process must be used to prioritize key metrics, interim measures, likely issues, and responses required in a disruption or failure scenario.
Drawing from his P&G operations excellence experience, Paul Bittinger reinforced Mike Wittman’s point that base reliability and predictability are paramount to ensuring that agility, visibility, and resilience measures don’t look like they are failing because of foundational reliability issues. He emphasized that that agility, predictability, and reliability do not mean “risk free!”
A best practice at CSL Behring under Paul McKenzie is their use of “smoke signals” as a metaphor used to signify degrees of disruption severity in their reliability management processes. Smoke signals are a great metaphor used at leadership levels to communicate how the degree of disruption impacts reliability. Smoke signal language is used to describe disruptive issues that are detected and analyzed in daily cross-functional business reliability meetings attended by the COO. These smoke signal issues are continually documented, analyzed for severity, and tracked to ensure that the right response thresholds are set, that the right level of attention is paid to the urgent issues that have been identified as impacting the patient and ultimate customer at the Moment of Truth. Bittinger emphasized that smoke signal analyses must be function and department agnostic to avoid negatively impacting the innovation capabilities, motivation, and effectiveness of cross-functional, problem-solving teams.
Bittinger said that while 80-90% of the supply chain must operate reliably and predictably every day, systems need to be in place to augment the analysis and track and trace processes implementing the corrective and preventative responses to disruptive issues as and when they occur.
Based on P&G’s consumer-driven supply network culture, all “issues and fixes” that disrupt customer OTIF are analyzed and prioritized “customer-back” according to their ultimate impact on the business Moment of Truth: meeting customer or patient needs on time and in full.
The panel emphasized the importance of six critical aspects in building agility and resilience:
1. Without a solid foundation of reliability and predictability, agility failures will be amplified.
2. Take a “patient back to supply” approach to “issue” analyses, seeing disruptions and their impact through the eyes of the patient.
3. Actionable, smart dashboarding and visibility of end-to- end supply chain key metrics; ensuring that they are contextually relevant and without Hau Lee’s “data distortion,” so they support the intelligent action and responsiveness to disruptions required for hyper-agility.
4. Accurate, harmonized, distortion-free and contextually relevant “issues” data for analysis and response.
5. Well-defined and clear response roles, standards, terminology, responsibilities, and collaboration processes for multi-disciplinary teams to efficiently resolve disruptive issues.
6. Top-down leadership must ensure that problems are systematically tracked and resolved and do not just return. Using clear language like “smoke signals” as an indicator of issue severity.
Lee closed out by emphasizing that agility is the intelligent and actionable sensing and accurate response to disruptive issues across the end-to-end business operating model, from supply through to the ultimate demand point: the patient.
Return to: The Patient-Driven Supply Network